Water leaks can cause severe damage to your construction and property, leading to expensive repairs, lost productivity, delay penalties, and increased insurance costs. Some insurers are hardening their stance, not even offering cover unless automatic controls are installed during construction. Installing Flow Management Devices can be a game-changer for developers, contractors, and property managers.
But where do you start? There’s no point having the best product if it’s not in the right place! In this series of articles, we'll explore the benefits of this innovative technology and how to specify it effectively.
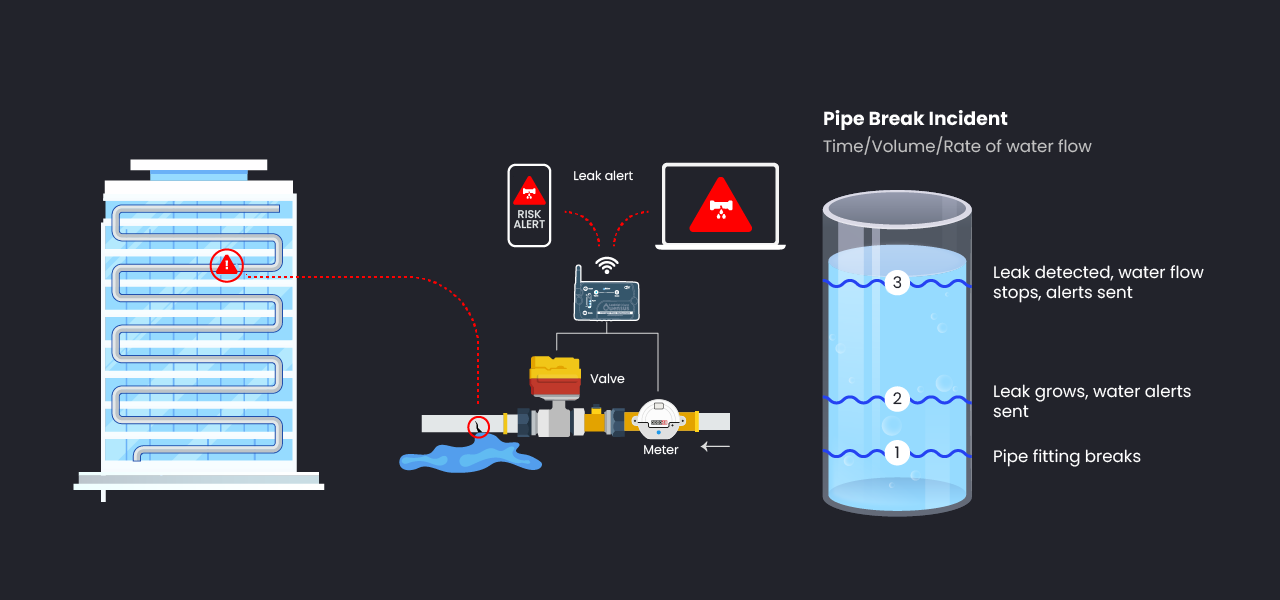
How does a system detect leaks
Often, we see specifications from insurers stating that “the equipment must be designed to automatically shut off the mains water supply to the insured premises in the event of an uncontrolled escape of water being detected, and not be reinstated until necessary remedial action has been taken to prevent further water damage losses”. On the face of it, this statement seems reasonable. However, how does the equipment/machine know that the event is due to "uncontrolled escape of water"?
There are usually 3 ways a machine would understand an escape of water event:
- Water contact sensors – either leak cable, leak tape or probes placed in any location water should not be present (like a fire alarm). This is a simple solution but relies on every single area to be monitored, sometimes making it cost prohibitive.
- Pressure monitoring – detect tiny leaks by measuring the decrease in pressure on a closed system over a period of time. The quicker the pressure decreases, the larger the leak. The longer the time period, the more sensitive the system is. This technique is very useful for closed systems such as heating circuits, but for mains water the valve and all outlets must be tightly shut-off so that the system becomes “closed”. The problem here is the valve must be closed for an amount of time to detect the change in pressure from beginning to end, and no water can be used during this period. A leaking toilet which is unfortunately common these days will cause false alerts using this method.
- Flow monitoring
A. Old generation (pre-2015), with human programmed thresholds – using a flow meter or flow switch. Different variables are used to measure and compare water consumption against pre-set thresholds which must be provided by a human. Thresholds which are commonly used include:
- Maximum time of one event
- Maximum volume of one event
- Maximum flow rate at any time
- Minimum temperature at any time
B. New generation (2015 onwards), with machine learning – all the features of option 3, but with the massive benefit of learning the unique consumption profile of the monitored area, making it autonomous and independent from the person installing it. No longer do you have to rely on guesswork to predict what the property will likely consume in a normal day. This enables much more accurate leak detection which gets better over time. Without needing a human to enter values, this also means that many more thresholds can be generated, making the system’s leak detection abilities far superior and supports the detection of small drips and monitoring around pre-existing leaks. Machine learning thresholds (which Quensus have developed) include:
- Maximum time of one event, depending on the day and time
- Maximum volume of one event, depending on the day and time
- Maximum volume within a time period, above a set flowrate
- Maximum volume within a time period, below a set flowrate
Of course, there are systems which incorporate a mixture of techniques which provides a solution for any scenario. Quensus currently use flow monitoring with machine learning, as well as water contact sensors, but we are also developing pressure monitoring using the power of AI anomaly detection to match patterns in the combination of flow and pressure with known leak patterns to provide the World with the next level of leak detection.
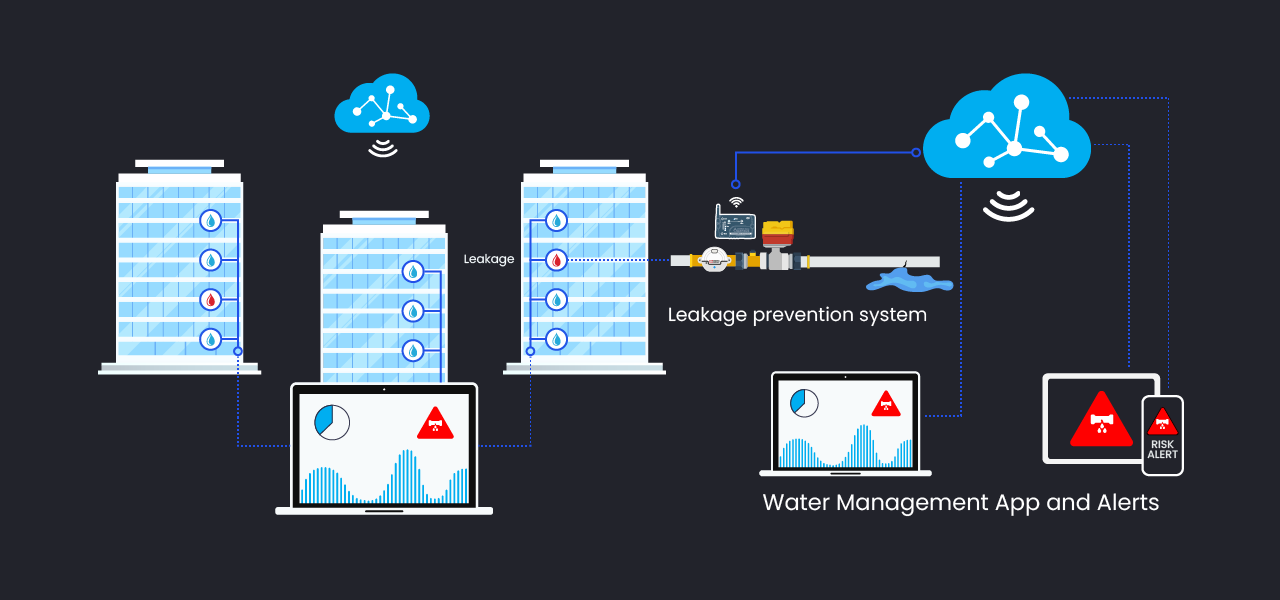
Specifying new buildings for Insurance Benefits
According to the Construction Insurance Risk Engineers Group Best Practice Guidance on Managing Escape of Water Risk on Construction Sites, a Water Management Plan for the temporary water supply and permanent works water systems should be made before works commence. The full specification can be found here.
Rapid detection and quick isolation using flow management devices are key to the mitigation of water damage. Specifically, automatic flow monitoring and shutoff devices should be installed on:
- Main temporary water supplies – see our SiteNet for Construction product
- Main permanent supplies – see our BREEAM solution
- Downstream from any storage tank (e.g. booster sets)
- On each floor of a permanent supply and/or each riser (if pipework is vertically fed)
- On any automatic refill system.
- Any other systems, including LTHW, MTHW, chilled water, underfloor heating, and irrigation.
Furthermore, because property insurers are also seeing substantial increases in losses due to escape of water events, you are also advised to plan for the continued use of permanent water management devices in the operational building too, to improve the availability of insurance, reduce the installation costs associated with retrofitting devices, and achieve the additional environmental benefits and cost savings for many years to come.
For more information on the products listed in the article, take a look at the links below:
- LeakNet Gen 2 - all-in-one leak detection/prevention solution with machine learning and automated shut-off and alert capabilities.
- Water contact sensors - including wireless splash sensors and leak detecting cables.
- FlowReporter App - designed for seamless water management for one or multiple buildings all in one place.